It’s not a secret that efficient processes are essential for companies to remain competitive and achieve sustainable growth:
- Streamlined operations enable businesses to maximize productivity and profitability by reducing waste, minimizing costs, and optimizing resource utilization ultimately backing up quality and customer satisfaction.
- Efficient processes provide the flexibility needed to adapt to changing market conditions, technological advancements, and evolving customer expectations.
At Sapling Financial Consultants, we specialize in helping companies enhance their operational efficiency, ensuring they can thrive in a dynamic business environment. Our expertise spans healthcare, manufacturing, technology, consumer products, logistics, and financial services, ensuring that we can deliver value in any sector.
Lean Six Sigma is a powerful methodology that combines Lean manufacturing principles and Six Sigma techniques to eliminate waste, reduce process variability, and improve quality. Lean focuses on streamlining operations and enhancing efficiency by removing non-value-adding activities, while Six Sigma emphasizes the reduction of defects and errors through data-driven decision-making. Together, they provide a comprehensive approach to optimizing processes, increasing productivity, and achieving sustainable business improvements.
Our process optimization expertise, combined with comprehensive business analytics and financial modeling services, unlocks value within your business. This data-driven approach quickly assesses your current situation, identifies improvement opportunities, and develops a strategic roadmap to enhance operational efficiency and reduce costs. The scalable methodology can be applied to a single process, department, division, or the entire business.
We offer tailored performance optimization services that encompass the full spectrum of Lean Six Sigma methodologies, including:
- Current State Analysis
- Assess and benchmark processes against industry best practices.
- Identify reasons for underperformance, non-value-adding activities (waste), and process errors.
- Determine root causes of errors and develop solutions.
- Process Optimization
- Redesign processes to eliminate waste and correct errors based on current state analysis insights.
- Continuous Monitoring
- Develop a framework for ongoing monitoring and feedback to sustain improvements and make data-driven adjustments as needed.
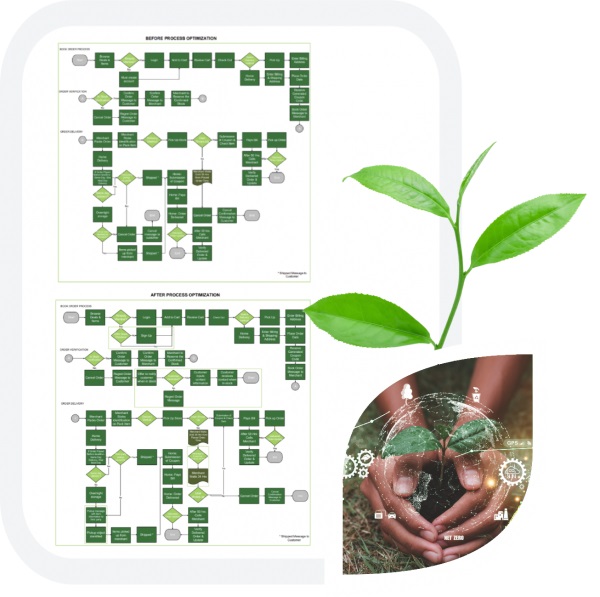